The development of new thermoactivated compounds has focused attention on the finishing of low-quality leather using release paper. With over 30 years of experience in the design and installation of finishing plants using release papers, Gemata has now been able to further the process with its innovative technology, providing environmental and cost benefits at the same time. The details of the technology are explained in the following schematic.
![]() |
Fig 1. Lay out Ecofinish - Finish line by using release paper |
Lay out Ecofinish shows the line proposed for finishing buffed, fullgrain leathers using release paper. The pre-buffing operations result in a uniformed leather surface which is smooth and free of defects. This can be obtained with just a light finishing. It results in a natural-looking product with excellent cutting yield. It is ideal for use in luxury footwear and handbags.
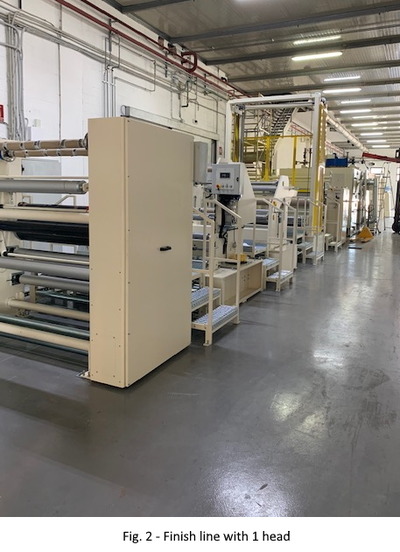
The use of ovens with a mix of infra-red and hot air technology allows perfect control of the temperature of the film applied to the paper. Pyrometric sensors constantly measure the film’s surface temperature to prevent bubbles appearing on the finished surface and overheating which would affect the durability of the release paper. It is a fully-controlled process that results in a reproducible and defect-free product.
The film on the paper is obtained by applying a PU resin in layers using two roller coating heads. Gemata’s decision to use roller coaters instead of a blade system has the advantage of guaranteeing perfectcontrol over the amount of product deposited, as well as not crushing the design on the paper, which makes it last longer. Gemata has concentrated on reducing costs and controlling the environmental impact of its processes, while keeping in mind the importance of the quality of the final results.
The adhesive is applied directly to the buffed grain using a spray cabin. This could be an alternative type of spray cabin should the client require a more compact line. Applying the adhesive solely on the leather surface rather than on the whole surface of the release paper saves 30% of the product compared to traditional systems. To reduce the risk of contamination of the finished article, there is a through-feed washing system at the exit of the spraying cabin, which consists of rotating brushes and wet-scraping devices.
The Gemata system thus eliminates the traditional dry scraping, creating a line completely free of dust contamination. The coupling of the leather with the release paper is achieved using a heated roller press. The pressure and temperature activate the adhesive on the leather, sticking it to the film previously applied to the paper. At the same time, the thermoadhesive expands slightly, sealing the defects on the surface of the leather. It is also possible to apply foam adhesive to increase the final yield of the finished leather, although this could affectits natural look and feel.
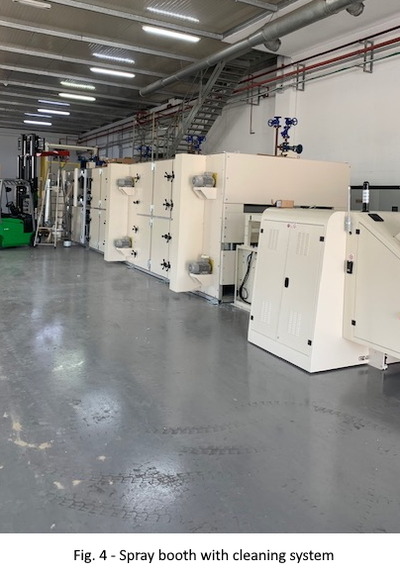
The use of an adhesive tape system to clean the release paper represents a further innovation compared to traditional systems. After the detachment of the leather from the release paper, residues of the chemical product remain in the areas of the paper which were not in contact with the leather.
As mentioned, a light finishing is used in the treatment of the buffed grain leather. As a result, the film on the paper is not completely pulled from the leather and so removed from the paper.
In the areas that do not come in contact with the leather, the film remains stuck to the paper and must be removed in a different way.
For this reason, a cleaning system is applied, with an adhesive tape which comes in contact with the release paper,completely cleaning the surface. Once rewound in the rewinding unit the release paper can be reused, either immediately or later on, without any further action. The line is equipped with all the necessary features to ensure the paper can be changed without plant downtime: an unwinder with two stations that are always ready for use; an automatic cutting unit and a storage unit with 30 metres of paper. This means the system is highly productive and easy to operate and maintain.
![]() |