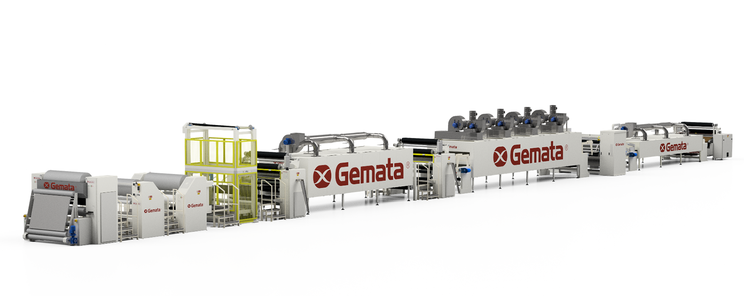
GREENFINISH is the innovative release paper finishing line with very low environmental impact. It is the first system to use the GREENSTARs roller coating machine to coat the chemicals on any kind of leather.
The standard line is complete with accumulator and allows non-stop processing 24/24, ideal for tanneries that have large production batches.
The unwinder, the rewinder and the cleaning machine unit are designed in separate modules to eliminate any type of interruption or downtime: on request, it is possible to increase the working speed, lengthening the infrared tunnels and adding a second head for the finishing of coarse grains.
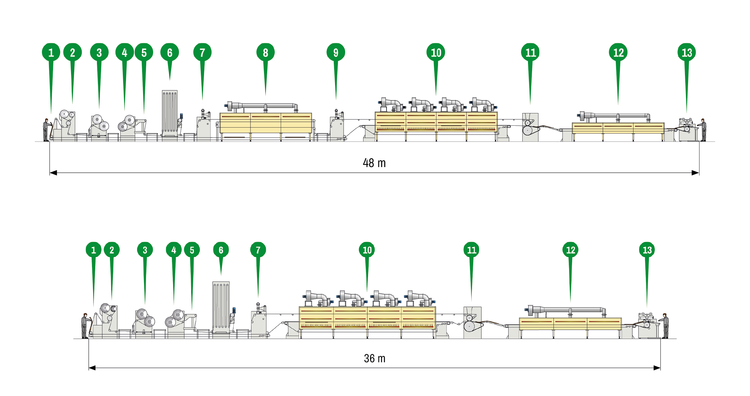
The line combines efficiency and eco-sustainability aspects:
- combine efficient and ecological performance;
- it creates a covering effect that evenly covers the surface of the leather;
- minimisation of negative environmental impacts with the reduction of energy waste and the elimination of atmospheric emissions.
Among the main innovations made by this finishing system are:
- the possibility of finishing any type of leathers, with a single step with considerable benefits in reducing costs and working times
- the possibility of obtaining an almost completely finished leather that can be customized with replacements and fixatives
- compared to spray and roller finishing, the reduction of finishing steps which, consequently, reduces the risk of contamination to a minimum
- the possibility of reusing the release paper, now consumed after 30 passes, also in an alternative way, i.e. as a matrix for products with smooth base (drummed or with larger prints).
THE SYSTEM
1.DETACHING CONVEYOR BELT: table to detach leathers from release paper.
2.RELEASE PAPER CLEANING MACHINE: unwinder and rewinder of the adhesive paper to remove residues of coated film after the detachments of the leathers.
3.REWINDING UNIT WITH DOUBLE COILS AND WITH CENTERING motorized unit for rewinding the clean release paper.
4.TWO-STATION FIXED UNWINDER: to unwind the coil of release paper which feed the finishing line.
5.JOINING TABLE: for paper locking and cutting .
6.PNEUMATIC ACCUMULATOR 30 m: storage of release paper to feed the line during the roll change.
7.GREENLINE-R ROLLER COATING HEAD: roller coating machine to coat the film on release paper with two rollers.
8.INFRARED DRYING TUNNEL: double chamber infrared drying tunnel.
9.GREENLINE-2R ROLLER COATING HEAD: roller coating machine to coat the film on release paper with two rollers.
10.DOUBLE STARDRIER-IR INFRARED DRYING TUNNEL: infrared tunnel to dry the chemical on the leather.
11.LAMINATION CALENDER: low pressure rotary press for release paper-leather lamination.
12.CONVEYOR BELT.
13.STARDRIER-IR INFRARED DRYING TUNNEL: infrared tunnel to dry the chemicals on the leather.
14.GREENSTARs ROLLER COATING MACHINE: roller coating machine to coat the chemicals on the leather.
ECONOMIC BENEFIT
- Low cost of the plant.
- Lower production cost.
- Only 3 people are required to run the system.
- No boiler for the diathermic oil.
- Reduced power consumption of drying ovens: the lamps are turned off during the line inactivity.
- Right to use the GREENFINISH® BRAND.
TECHNICAL BENEFIT
- Small overall dimension
- Upgrading of any type of leather.
- Temperature control directly on both the surface of the release paper and on the leathers.
- Elimination of dust contamination.
- Automatic cleaning system for release paper.
- Possibility of use of different types of release paper.
GREEN BENEFIT
- Reduced power consumption of water and electricity.
- No waste of chemical.
- Re-use of the release paper from 80 up to 90 times.
- Zero emissions in atmosphere.