SPRAYSTAR EVO is an innovative spraying booth fitted with spray guns, designed for finishing all types of leather used in the automotive, upholstery, footwear, and clothing industries.
SPRAYSTAR EVO is available with working widths of 1800, 2200, 2600, 3000, 3400, and 3800 mm and in dry or water curtain versions. It is set up to work with any kind of high and low-pressure spraying system (HVLP, AIRLESS, AIR-MIX, etc.).
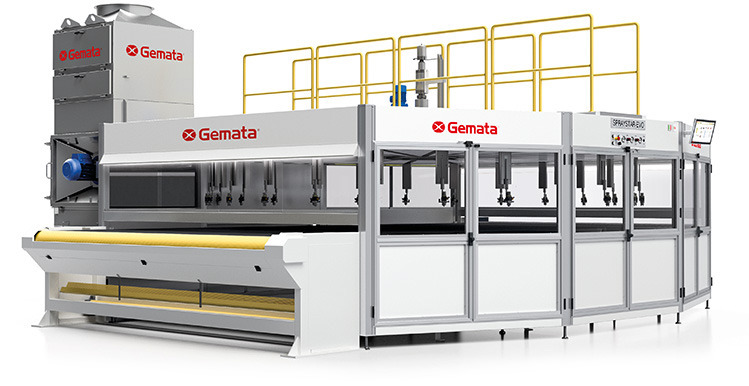

Emissions 10 times lower than legal limits

10% less air to extract thanks to the hexagonal design

8-24 arms, up to 3 different spray guns each

Compatible with chichen wire or perlon thread conveyor system

Even leather coverage with minimized overspray
The spray booth
The octagonal design of the booth reduces air extraction volume by 10% compared to traditional rectangular booths and prevents fume stagnation. The interior is easily accessible thanks to the six large front doors and sliding glass windows. The placement of the distributor shaft above the carousel outside the spray-booth prevents product dripping onto the leather. The walkable platform with railings allows safe and efficient access for maintenance.
MODEL | 1800 | 2200 | 2600 | 3000 | 3400 | 3800 |
---|
The rotary carousel
At the core of the spraying system is the rotary carousel, available with 8, 12, 16 or 24 arms. Up to three independently fed spray guns can be mounted on each arm. Robust and highly versatile, it is set up to work with all types of high and low pressure spraying system (HVLP, AIRLESS, AIR-MIX). The spray gun holders are height-adjustable and entirely built in AISI 304 stainless steel.
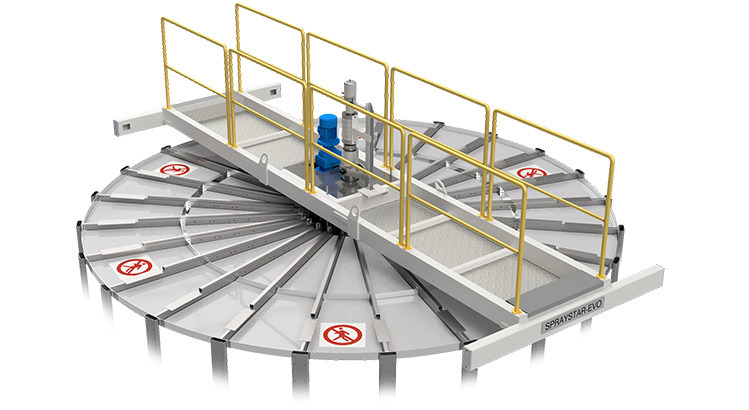
Rotary carousel and operator platform with safety railings for distributor shaft access.
The modular distributor shaft
The modular distributor shaft, available with 5 or 9 ways, allows higly-flexible configuration of spray circuits. It supports Airless, HVLP, and recirculating or non-recirculating systems, managing different quantities and types of circuits. Thanks to its two-section design, different working pressures can be combined, and the air and color chambers can be controlled independently. This also makes maintenance and seal replacement easier. Large internal air channels help reduce spraying pressure by up to 25%, improving overall efficiency.
Smart Spray Control
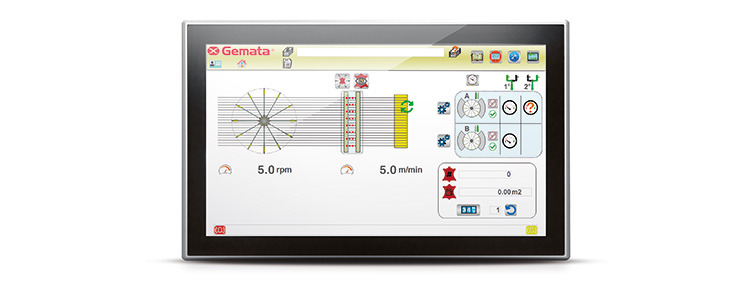
SPRAYSTAR EVO is equipped with Smart Spray Control (SSC), an advanced economizing system that eliminates waste and ensures real-time monitoring of the entire spraying process.
The intuitive software interface of Smart Spray Control is easy to use and it is configurable via a large touchscreen panel. A main synoptic screen allows real-time monitoring of the system’s status, giving the operator complete and immediate control. With Smart Spray Control, machine parameters and recipes can be changed and made available to remote systems for analysis and/or adjustment (Industry 4.0), along with crash logs, historical data and usage statistics.
The traditional spraying process
In traditional spraying systems, the leather profile detected at the infeed by a reading bar, is enlarged to ensure proper chemical product coverage along the leather edges. Spraying is triggered when the spray gun nozzle axis intersects the edges of this enlarged profile. As illustrated, this method leads to unnecessary oversprays outside the actual leather surface.
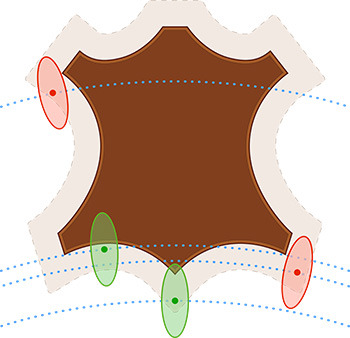
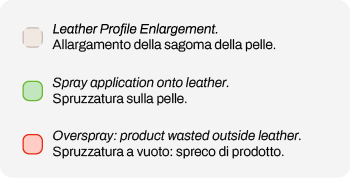
The SSC spraying process
The SSC system precisely manages the entire spray area of each spray gun by comparing it with the actual leather profile detected at the infeed. Spray guns are activated only when the operator-defined overlap threshold is exceeded. This ensures uniform edge coverage, eliminates overspray on empty areas, and significantly reduces product waste.
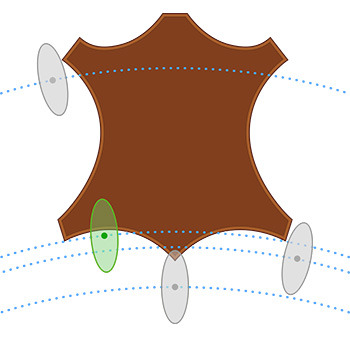
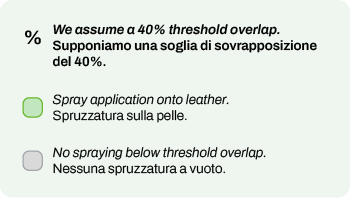
Eco Scrubber
ECO SCRUBBER is Gemata’s most advanced and environmentally friendly purification system, specifically designed for the abatement of fumes generated inside spray booths.
Compared to conventional market technologies, it filters out 98% of particles with a size of 10μm, reducing atmospheric emissions by approximately a factor of 10. ECO SCRUBBER achieves this exceptional filtration performance thanks to:
- Innovative modification of spherical packing elements
Their size has been almost halved, doubling the contact surface area exposed to the fume stream. The number of elements has been significantly increased from 4,500 to 36,000 units. - Integration of a diagnostic system
Optional - Addition of a dry filter unit
Optional
The conveyor systems
With the perlon string system, hides are supported and conveyed by a series of parallel nylon strings, ensuring stable transport with minimal maintenance. In case of breakage, each string can be replaced individually. The system includes a string scraper for cleaning. Alternatively, a string washing system [optional] is available, providing continuous cleaning to prevent contamination and the dispersion of dust into the air.
With the chicken-wire system , hides are supported and conveyed by a plastic mesh, which ensures uniform and stable transport. This solution guarantees the total absence of dust contamination. In addition, dry chemical residues can be easily detached from the mesh once a week and rolled up for disposal as common dry waste. The mesh can be quickly replaced every two to three months and disposed of as regular dry waste, resulting in significant cost savings.